- Messages
- 7,883
- Location
- Near Lutterworth, Leics.
Cleaned the YTS-23 yesterday/today.
Complete disassembly apart from removing the springs or pads, the first time I've done this and a little nerve wracking!
On close inspection it looked as though someone had spayed it with spray mount and then shaved over it!
Went well though, and I only had to take off a few keys/rods when re-assembling due to not doing it in the right order.
Some of the pads looked a little past their sell by date.....
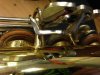
Once off the sax I coated them in Auto Glym Leather Care Cream and left overnight to soak in. I've used this successfully before on sorry looking pads when sprucing up the Old Russian Tenor.
Body and key metalwork cleaned with electroplate cleaner and isopropyl alchohol (not mixed!).
New cork needed on two palm keys and a few elsewhere. Stopped the clattering which had been there previously. Once assembled I used a cocktail stick to sparingly oil all the keys/rods with Selmer Key Oil.
All in all a pleasing if rather time consuming pastime. Off to Connolly-MIR to get a few dings sorted in the week then it'll be almost as good as new.

Complete disassembly apart from removing the springs or pads, the first time I've done this and a little nerve wracking!
On close inspection it looked as though someone had spayed it with spray mount and then shaved over it!
Went well though, and I only had to take off a few keys/rods when re-assembling due to not doing it in the right order.
Some of the pads looked a little past their sell by date.....
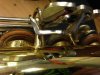
Once off the sax I coated them in Auto Glym Leather Care Cream and left overnight to soak in. I've used this successfully before on sorry looking pads when sprucing up the Old Russian Tenor.
Body and key metalwork cleaned with electroplate cleaner and isopropyl alchohol (not mixed!).
New cork needed on two palm keys and a few elsewhere. Stopped the clattering which had been there previously. Once assembled I used a cocktail stick to sparingly oil all the keys/rods with Selmer Key Oil.
All in all a pleasing if rather time consuming pastime. Off to Connolly-MIR to get a few dings sorted in the week then it'll be almost as good as new.